Cómo mejorar la eficiencia productiva de tu línea de embalaje con el OEE
Uno de los mejores indicadores para evaluar y mejorar la eficiencia de los equipos de una línea de embalaje es el OEE (Overall Equipment Effectiveness o Efectividad total de los equipos). Se trata de un KPI clave para medir la productividad de todos los procesos y sistemas productivos de una empresa y un imprescindible para el final de línea automatizado. El OEE es una métrica muy ligada a la filosofía de empresa de mejora continua, metodología Lean y la Industria 4.0.
En el artículo de hoy analizaremos el OEE desde el punto de vista de una línea de embalaje, y veremos las claves y pautas para mejorar su la eficiencia de la línea.
¿Qué es el OEE y cómo afecta a mi línea de embalaje?
El OEE mide la eficacia de los equipos productivos mediante un cálculo de varios parámetros de rendimiento de la maquinaria. Gracias al cálculo de este indicador las empresas pueden conocer sus puntos débiles de pérdidas de productividad, cuellos de botella, paradas innecesarias e incluso errores y rechazos. De esta manera es más ágil para la empresa implementar mejoras, aumentar la calidad de la producción y en definitiva el nivel de satisfacción de sus clientes que se produce al reducir tiempos de entrega de la mercancía, eliminación de unidades defectuosas etc.
En una línea de embalaje final es esencial conocer el OEE para aumentar la productividad y la rapidez de la línea, reducir errores en el embalaje, mejorar la calidad de enfardado, etc.
¿Cómo se calcula el OEE y cual es el indicador óptimo?
El OEE tiene en cuenta tres variables: disponibilidad, rendimiento/velocidad y calidad, que se multiplican para conseguir el coeficiente de rendimiento final. Veamos cómo se aplican en una línea de embalaje:
Indicador de Disponibilidad:
La disponibilidad del equipo se calcula dividiendo el tiempo productivo (tiempo en el que los equipos funcionan sin paradas) por el tiempo planificado de producción (o su disponibilidad teórica). En este punto no se incluirían paradas planificadas (festivos, cierres de la línea por mantenimiento planificado, etc).
En una línea de embalaje se puede contar como tiempos no productivos los cambios de consumible (film, fleje, etc), paros por cambios de turno, paradas en la línea por averías o errores, cambios de formatos de palet que conlleven pausas en el proceso, etc.
El resultado será la pérdida de disponibilidad de la maquinaria por los paros en la producción.
Indicador de Rendimiento
Este indicador de rendimiento o velocidad se obtiene al dividir el tiempo productivo real (obtenido del cálculo de disponibilidad) entre la producción teórica definida según el rendimiento máximo de la maquinaria o según el propio proceso de la línea.
En una línea de embalaje, por ejemplo, se calculará el tiempo real de producción de la línea dividido por las producciones máximas de los diferentes sistemas de embalaje.
La cifra obtenida de este indicador es la pérdida de rendimiento o los excesos de tiempo de producción de embalaje.
Indicador de Calidad:
Por último el parámetro de calidad es el resultado de dividir el tiempo de producción buena (quitando paradas, piezas defectuosas, etc) entre el tiempo teórico para producir según el rendimiento máximo de la máquina (producción real esperada). Es decir, en una línea de embalaje dividiremos la producción de los palets embalados correctamente (sin fallos), por el tiempo de producción real genérico de todos los palets que han salido por la línea.
De esta manera se obtiene la pérdida del tiempo que se han invertido en producir unidades con defectos o rechazadas.
El indicador final del OEE
El resultado de la efectividad total de la máquina, incluyendo pérdidas, se obtiene al multiplicar los tres indicadores de disponibilidad, rendimiento y calidad. El indicador final se expresa en porcentaje, con un valor entre 0 y 100%, siendo obviamente el 100% el resultado más que óptimo de producción en que sólo se fabrican piezas buenas, a la máxima velocidad y sin paradas.
Un indicador mínimo de OEE es que éste se situe por encima del 70%, ya que por debajo de esta cifra supone que la empresa tiene bastantes rechazos, mercancía defectuosa, averías y paradas constantes en sus líneas productivas, suponiendo una gran pérdida de dinero. De hecho, superar el 85% de OEE sería el porcentaje necesario para conseguir la excelencia World Class Manufacturing, un gran hito para muchas empresas
A continuación te incluimos un gráfico para calcular el OEE, según el desglose de los tiempos de tus equipos de embalaje:
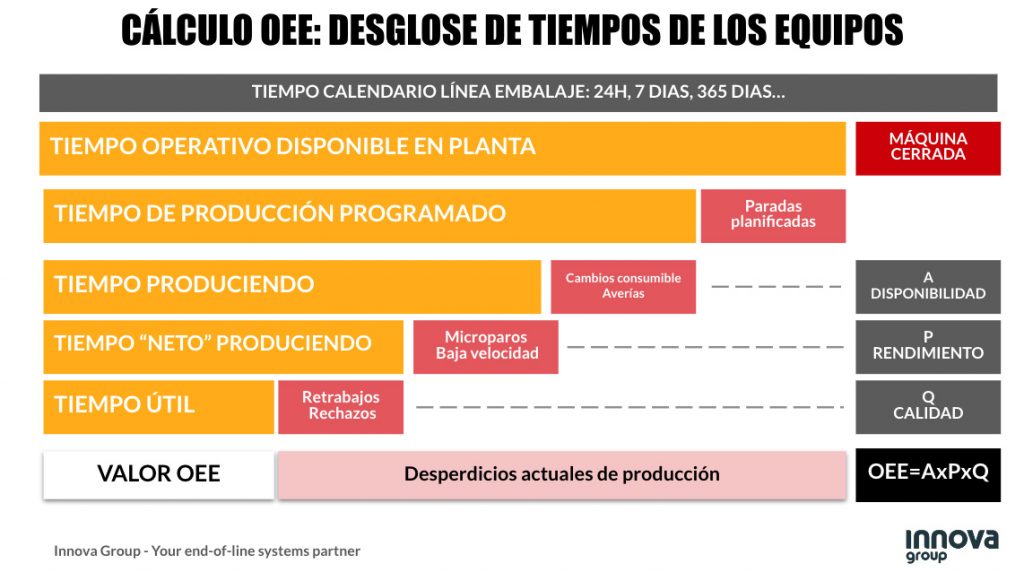
¿Cómo mejoro la eficiencia de mi línea de embalaje y el OEE?
Hay muchos aspectos que influyen a mejorar el coeficiente de eficiencia de la línea, y cuando el OEE tiene mucho margen de incremento hay algunas acciones correctivas que pueden resultar en un mejora bastante rápida a corto-medio plazo.
Desde nuestra experiencia cómo fabricantes de sistemas para el final de línea y nuestra metodología Lean Manufacturing te detallemos algunas acciones y pautas clave para mejorar la eficiencia:
- Renovación de equipos obsoletos y automatización: Una de las acciones más obvias es la renovación de sistemas de embalaje que estén provocando muchas paradas y averías constantes. En el caso de tener procesos no automatizados, también es recomendable invertir en sistemas de embalaje automáticos por sus múltiples beneficios y rápida amortización comparándolos con las pérdidas y lentitud de los procesos manuales.
- Mantenimiento preventivo: el mantenimiento es esencial no sólo para reducir paradas de los equipos de embalaje causados por averías, sino también para mejorar su rendimiento. En este punto ese esencial que el plan de mantenimiento se planifique de manera que no afecte también en una gran parada de la línea y que se realice en paradas ya planificadas (estacionales, festivos, etc).
- Servicio directo del fabricante: Es recomendable que el fabricante de los equipos (OEM – Original Equipment Manufacturer) sea tu proveedor también de los servicios de mantenimiento, soporte técnico, etc No sólo en rapidez y reducción de las paradas sino en su amplia experiencia en la línea para obtener un mejor embalaje de tu mercancía (mejor protegido, más seguro para el transporte, etc).
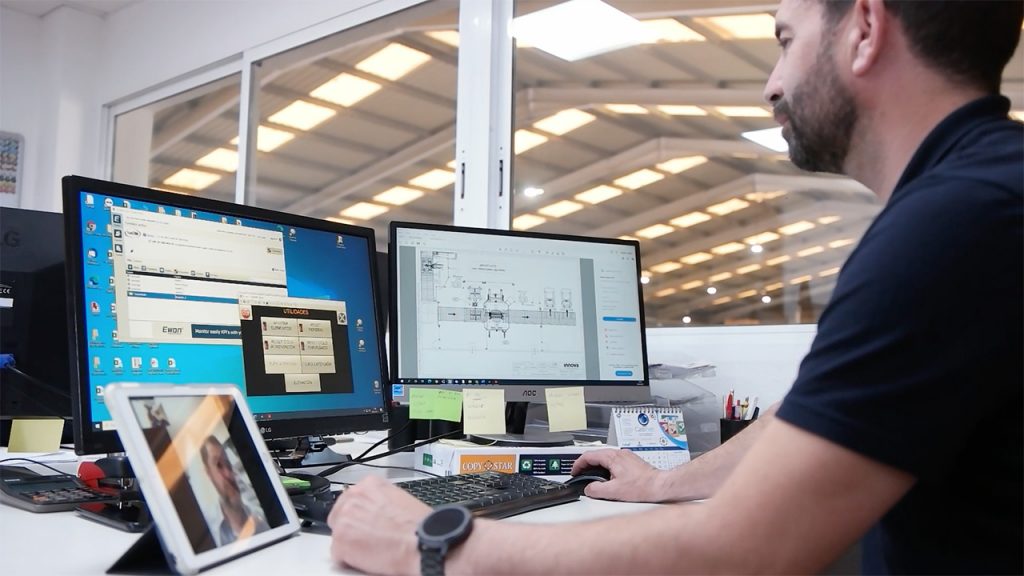
- Repuestos inmediatos: Ya sea a través de un fabricante que provee el servicio o con stock propio de repuestos, se trata de un componente clave para reducir las paradas por cambios de piezas.
- Control de calidad del embalaje: si la empresa no lo posee este es un punto de mejora inmediato que hará incrementar el indicador OEE. Se trata de aplicar planes de control de calidad en el proceso de embalaje para garantizar que la mercancía cumple con los estándares de calidad exigidos para el transporte y/o por el cliente. Una vez detectados los fallos y rechazos, éstos se pueden subsanar con la ayuda del fabricante y su servicio de mantenimiento.
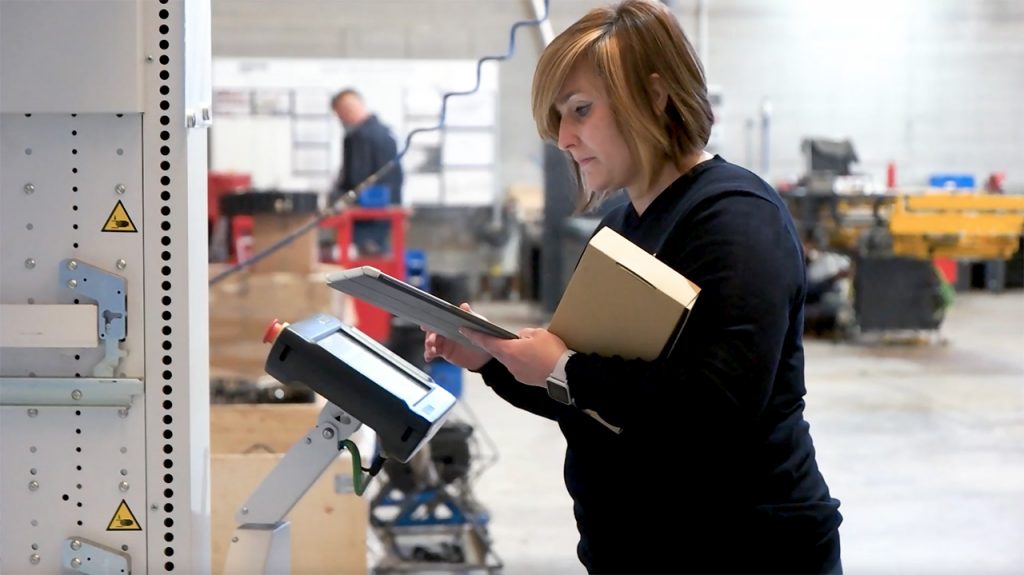
- Plan de formación continua: Otro punto clave es que el personal técnico de la línea obtenga formación especializada en el funcionamiento, cambios de consumibles y reparación de averías comunes. Es importante que el personal reciba formación no sólo en la puesta en marcha de la línea sino periódicamente según cambios de personal y actualizaciones en la maquinaria.
- Cambios de consumible más rápidos: Otro aspecto propio de los sistemas automáticos es que facilitan el cambio de film o fleje para reducir al máximo el tiempo de parada. En Innova por ejemplo ofrecemos sistemas con varias bobinas, cómo la envolvedora con doble carro o el Sistema Stretch Hood con 3 bobinas de film, para poder ofrecer mayor continuidad en la línea sin paradas por cambio de film. También escogiendo un sistema de embalaje en lugar de otro se consiguen reducir estas paradas: mientras que una envolvedora de palets convencional enfarda entre 150-200 palets sin cambio de film, el sistema Stretch Hood permite enfundar unos 1.000 palets al usar menos plástico por palet y bobinas con mayor cantidad de film.
- ¡Que no pare la máquina!: Como en las antiguas locomotoras de vapor es recomendable que las máquinas no tengan demasiadas paradas, y prolongadas en tiempo. Una máquina que está en constante producción va a tener menores problemas por llevar un mantenimiento más constante (engrase y limpieza de piezas) y en definitiva mejor funcionamiento.
En resumen, como hemos visto hay muchos parámetros que permiten mejorar la eficiencia de una línea de embalaje, también aplicables a cualquier línea de producción. Es importante tener en cuenta este coeficiente de mejorar continua para controlar mejor las pérdidas “invisibles” (de tiempo y desperfectos de mercancía) que al final del año pueden convertirse en un problema de producción e incluso de facturación para la empresa.
En Innova Group, cómo fabricantes especializados en líneas de embalaje automáticas, te podemos asesorar en la optimización de tus equipos de embalaje, consumibles y reducción de errores y paradas. No dudes a consultar sin compromiso con nuestro equipo técnico comercial.
¿Te interesan nuestros artículos técnicos sobre embalaje y logística? ¡Suscríbete a nuestra Newsletter técnica mensual!